Expanded Geotechnical offers foundation solutions expertise across the UK. We have a rich history of geotechnical experience and knowledge. We provide expertise in a range of piling techniques using the very latest rigs and technology. Our fleet is one of the youngest in the country, and includes Tier 4 engines, with market leading emissions performance.
We also offer a highly skilled temporary works department, materials technology centres in Manchester and London, geotechnical design, land surveying specialist teams, reinforcement detailing. We use the latest digital technologies to implement a state of the art digital build before any manufacture or construction commences to ensure absolute certainty during project delivery.
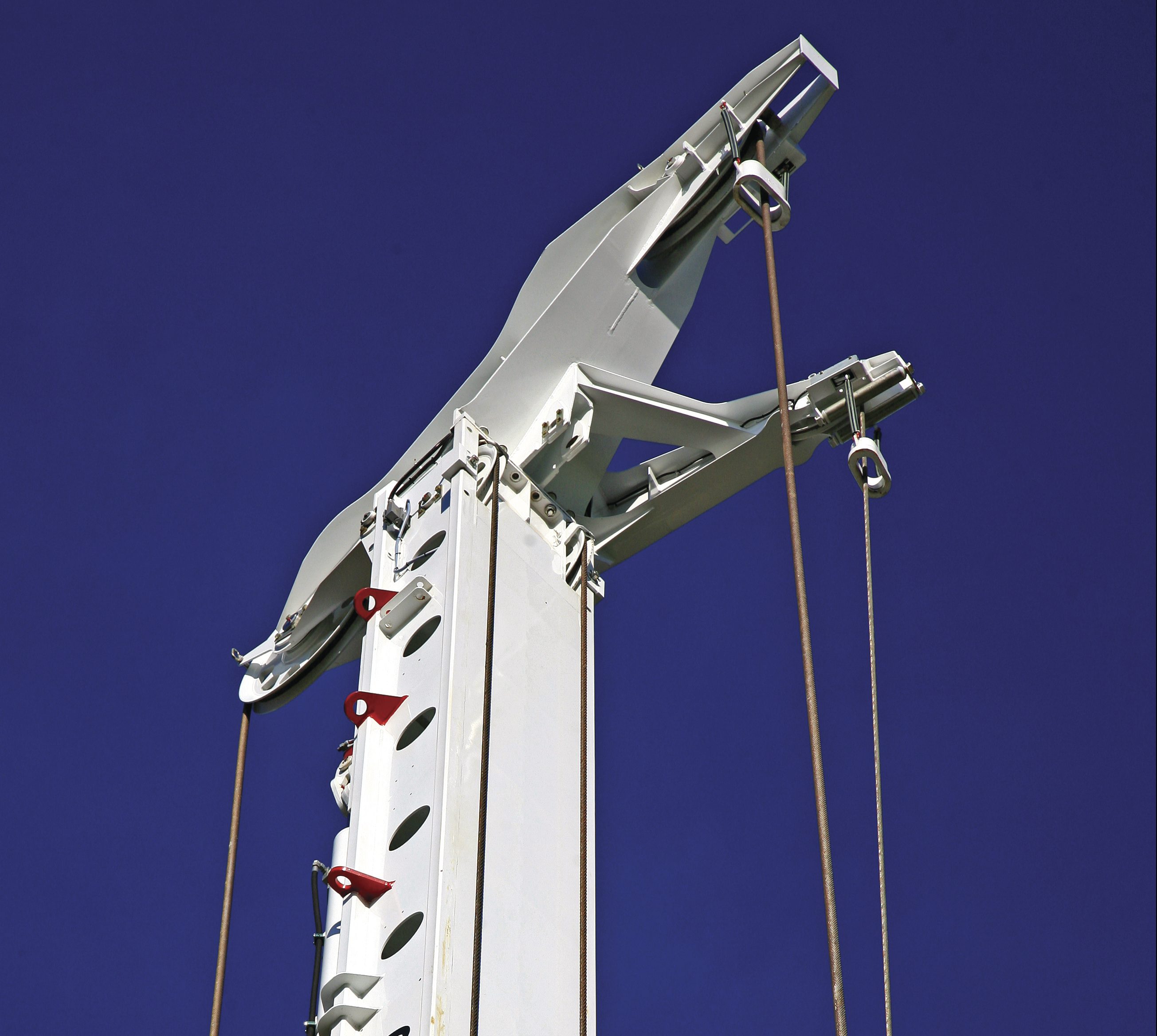
Expanded Geotechnical offers foundation solutions expertise across the UK. We have a rich history of geotechnical experience and knowledge. We provide expertise in a range of piling techniques using the very latest rigs and technology. Our fleet is one of the youngest in the country, and includes Tier 4 engines, with market leading emissions performance.
Our offering includes Rotary augered piles / large diameter capability, CFA including deep / large diameter capability, Secant and contiguous retaining walls, Plunge column piles, Diaphragm walls, Restricted access piling, Pile extraction / removal, Slurry wall, Support fluid and polymer expertise, Rock and obstruction coring, Sheet piling and Marine works.
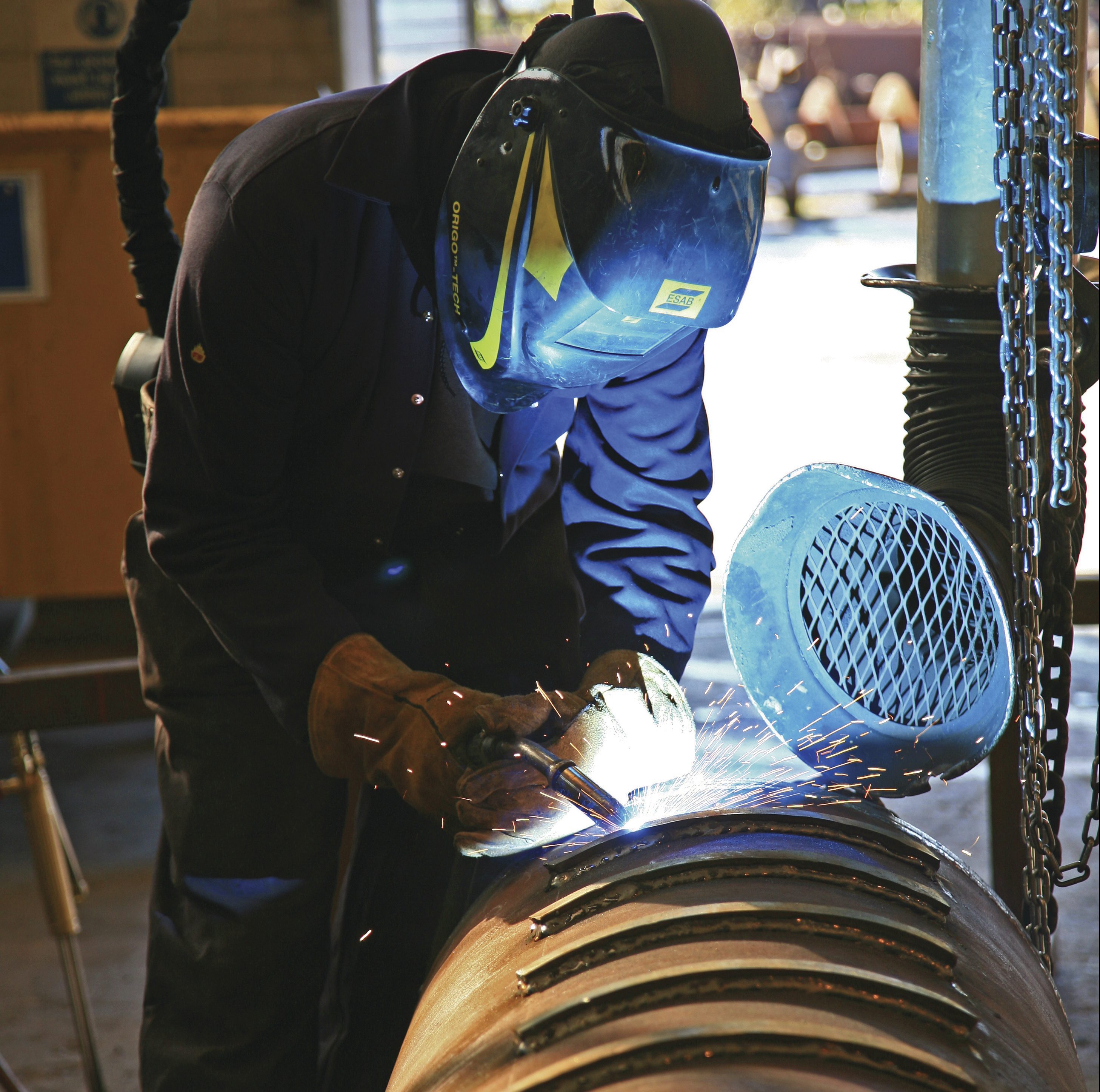
We also offer a highly skilled temporary works department, materials technology centres in Manchester and London, geotechnical design, land surveying specialist teams, reinforcement detailing. We use the latest digital technologies to implement a state of the art digital build before any manufacture or construction commences to ensure absolute certainty during project delivery.
Suite of testing offered through Expanded:
- Concrete pre-contract trials i.e. L-box, Bleed test, Chloride migration
- Concrete conformity testing i.e. Flow tests, cube test
- Low strain integrity testing (PIT)
- Crosshole Sonic Logging (CSL)
- Thermal Integrity Profiling (TIP)
- Fibre optic profiling
- Shape arrays monitoring (SAA)
- Inclinometer monitoring
- Static Load testing up to 30mN as standard
- Dynamic load testing
- Noise, Vibration and Dust monitoring
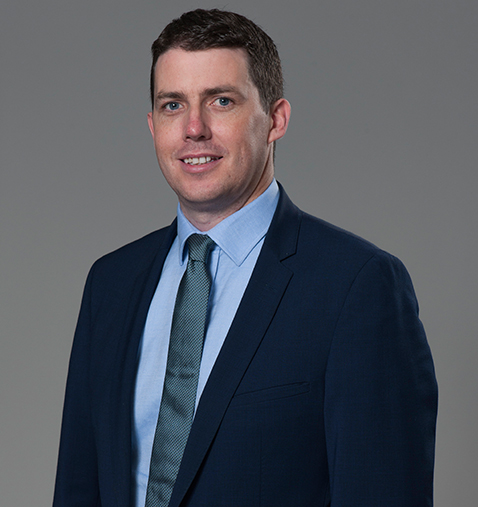
Appointed to lead Expanded’s concrete structures and geotechnical business, Peter has almost 20 years expertise, during which he has acquired an extremely broad skillset gained on a range of large scale projects such as Crossrail, London’s Leadenhall Building and most recently on Newfoundland, an iconic residential scheme on the Canary Wharf skyline.
As a qualified Civil Engineer, known for his ability to rise to complex challenges, he leads teams that focus on both learning, and delivering, efficient and innovative solutions. Known to empower and nurture talent, he fosters a culture on projects where a broad range of skills and competencies are shared, from steel frame, top-down construction, cofferdam construction and the delivery of Design for Manufacture and Assemble (DfMA) solutions in various sectors.
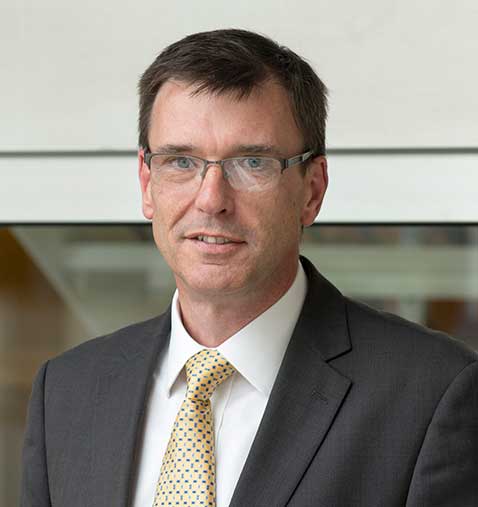
John Chick joined Expanded as Business Leader Geotechnical in 2015 with over 30 years’ experience in piling and ground engineering. John’s experience encompasses all bored and driven piling techniques plus marine piling, dockyard and flood defence engineering. Early in his career John was one of the first UK exponents of pile integrity testing, dynamic load testing and finite element analysis. He was a contributor to and reviewer of the CIRIA report on Pile integrity testing. This work has resulted in a lifelong interest in the many and various factors instrumental in the safe, successful construction of foundation piles. Johns background is in design and operations and after completing a MSc in Construction Management developed a major interest in business behaviours and team leadership. The development and growth of team members is fundamental to maintaining a sustainable business, which is effective for clients and engaging for the team members themselves. John has introduced a number of piling innovations throughout his career and led the delivery of projects valued from a few thousand to several million pounds. Always keen to meet customers John is available for early discussions as well as throughout projects and is always keen to hear feedback on our performance.

Matt currently leads the Expanded Geotechnical operations team nationally, overseeing all piling and ground engineering contracts, with full responsibility for project delivery. Matt ensures consistency in approach across the country and facilitates the support of the sites by our in-house teams ranging from procurement and quality assurance to administration and temporary works.
Matt joined the business in 2013 as Southern Area Operations Manager. With over 20 years’ experience in the foundations industry, Matt has a proven ability to run multiple contracts, delivering them safely, to a high standard and within budget.
Matt has directly overseen contracts involving many different piling techniques, including mini piling, large-diameter continuous flight auger (CFA), large-diameter rotary – with and without support fluid – and rotary cased secant, CFA secant and diaphragm walls.
Matt takes extreme pride in the dedication and calibre of the people that form his team. He has developed the operations
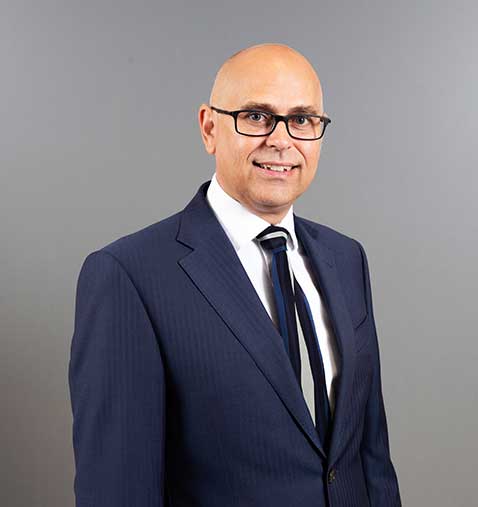
David joined Expanded Piling’s estimating team in January 2004, to provide proactive support during pre-construction stages of project development for prospective clients and stakeholders in the southern UK.
In parallel with the growth of the business unit since 2004, David’s role in Expanded Geotechnical widened to include management of a dedicated and enthusiastic work-winning team. David has been instrumental in the successful award of many prestigious foundation projects.
Working within the UK piling industry for almost 3 decades, David’s pragmatic and candid approach to problem-solving has been influential in developing and communicating, advanced and cost-effective foundation solutions. His collaborative and methodical style ensures the team’s knowledge and experience are brought together to develop effective foundation proposals.
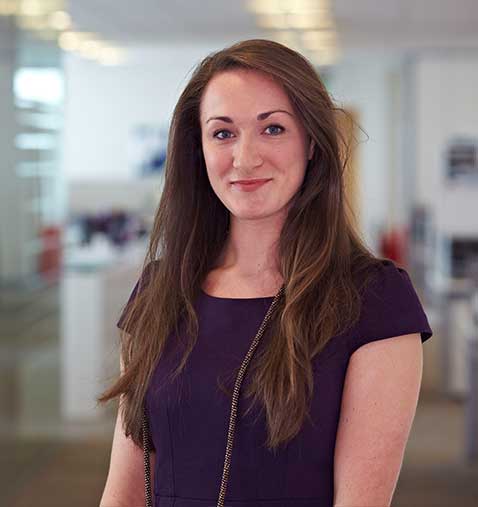
Since joining Laing O’Rourke in 2005, Hannah has progressed from Quantity Surveyor to Commercial Leader and has experience in the successful commercial delivery of schemes across various sectors, from tender stage through to completion. With roles held in both the Laing O’Rourke Construction and Expanded Geotechnical businesses, Hannah has experience as both Main Contractor and Subcontractor, with expertise in risk management, change management, cost management and negotiation of contracts.
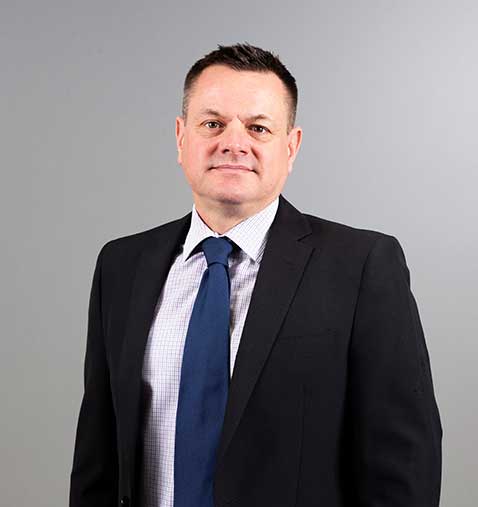
A highly motivated individual with over 20 years geotechnical design experience and a proven track record in delivering ground engineering solutions at all levels. Dr Toby Hayward joined our Expanded business in 2005. He manages the design team at Expanded Geotechnical and leads the geotechnical research and development. He is also a member of the FPS technical committee. He has extensive experience in geotechnical engineering with particular emphasis on the design and analysis bored piling systems and embedded retaining walls. He is experienced in the design of deep basements, bearing piles, ground anchors, slope stability analysis and general geotechnical processes. His experience gained on ground engineering projects has provided him with an in depth understanding of geotechnical, structural and soil- structure interaction problems and an ability to provide various solutions to UK ground engineering problems. He also actively supports the development of younger engineers through our graduate development programme.
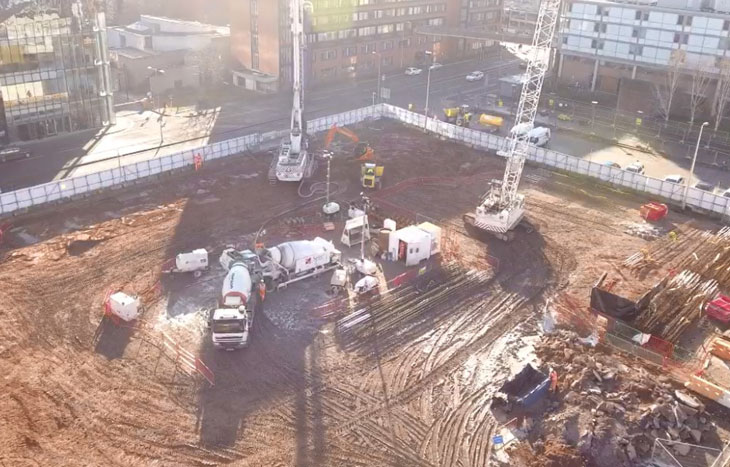
- BECKTON SEWAGE TREATMENT PLANT
- MANCHESTER ENGINEERING CAMPUS
- SOUTHALL WATERSIDE
- SOUTH QUAY PLAZA
- 250 CITY ROAD
- OXFORD WESTGATE
- LONDON DOCK
- THE FRANCIS CRICK INSTITUTE
- ONE BANK STREET
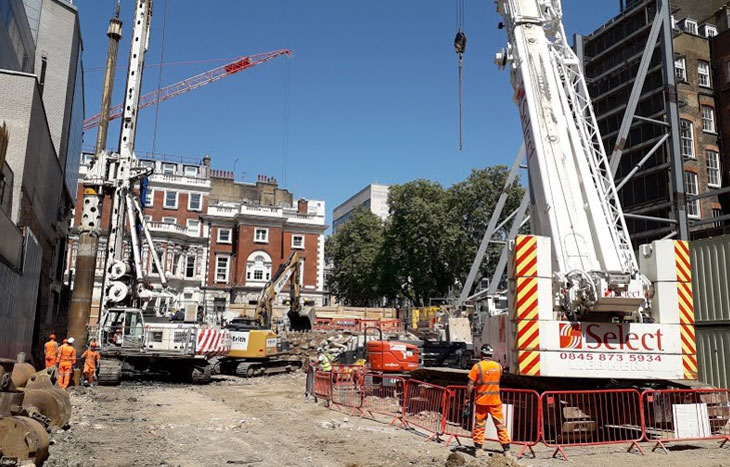
- NORTHERN LINE EXTENSION
- CLARGES, MAYFAIR
- THE FRANCIS CRICK INSTITUTE
- NINE ELMS SQUARE
- CANARY WHARK CROSSRAIL STATIONBOX
- PADDINGTON SQUARE
- 22 HANOVER SQUARE
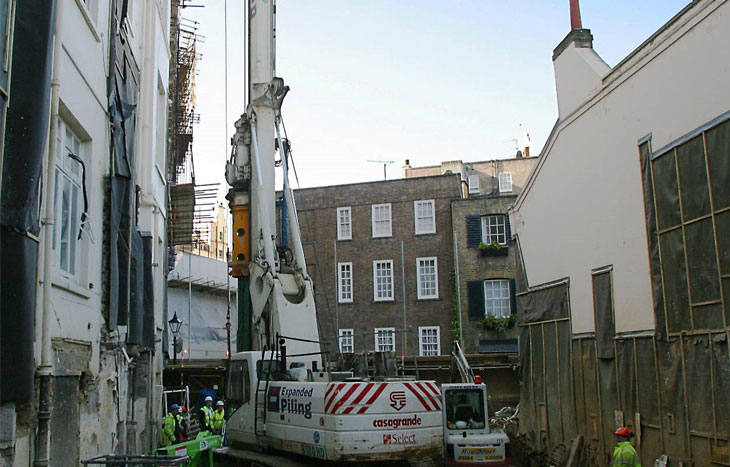
- NORTON BRIDGE
- WATFORD CHARTER PLACE
- CROSSRAIL AT LIVERPOOL STREET STATION
- 3-10 GROSVENOR CRESCENT
- THAMES TIDEWAY TUNNEL - ALBERT EMBANKMENT
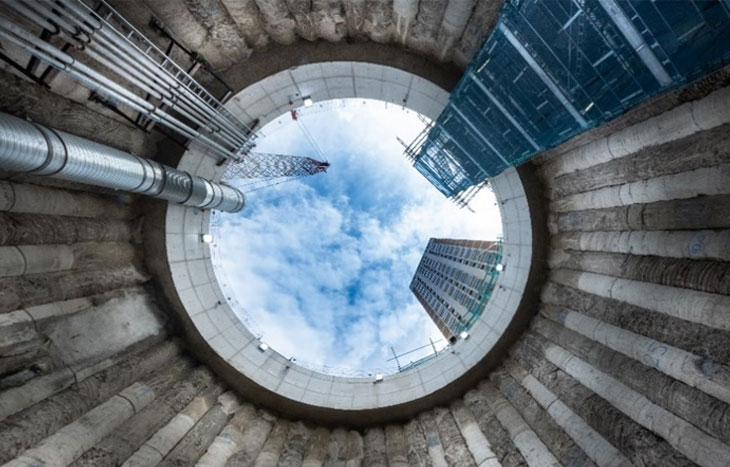
- THAMES TIDEWAY TUNNEL - ALBERT EMBANKMENT
- THAMES TIDEWAY TUNNEL - CREMORNE WHARF DEPOT
- THE FRANCIS CRICK INSTITUTE
- NORTHERN LINE EXTENSION
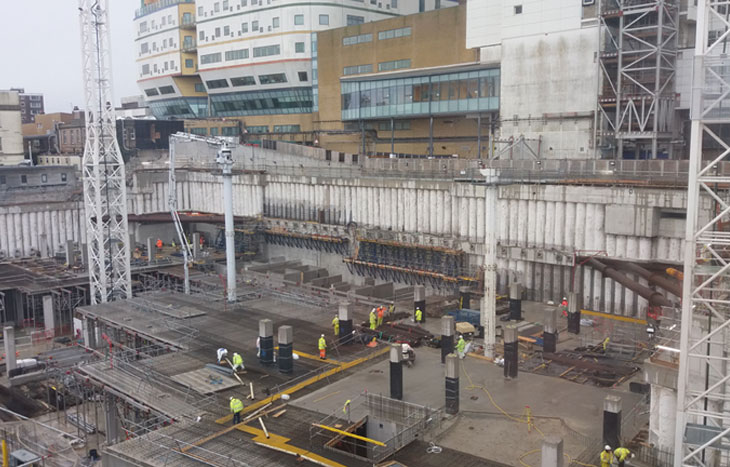
- WOOD WHARF MARINE PILES
- NORTHERN LINE EXTENSION
- WANDSWORTH RIVERSIDE QUARTER
- CANARY WHARF CROSSRAIL STATIONBOX
- SOHO PLACE
- PADDINGTON SQUARE
- EDINBURGH ST JAMES
- 22 HANOVER SQUARE
- KINGSGATE AND ZIG ZAG BUILDINGS
- ROYAL SUSSEX COUNTY HOSPITAL
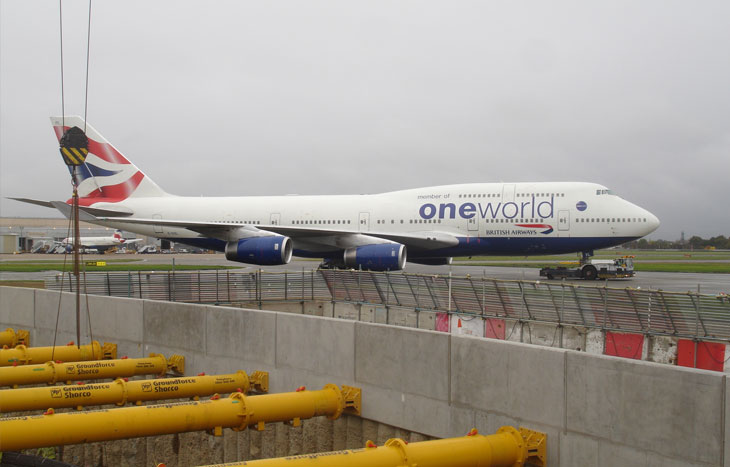
- HEATHROW EASTERN APRON
- OXYGEN TOWERS
- TTT, BLACKFRIARS BRIDGE
- EDINBURGH ST JAMES
- OXFORD PHYSICS, BEECROFT
- NINE ELMS SQUARE
- OXFORD BIOCHEMISTRY
- NORTHERN LINE EXTENSION
- GOOGLE HQ, KINGS CROSS
- BRUNEL BUILDING, NORTH WHARF ROAD
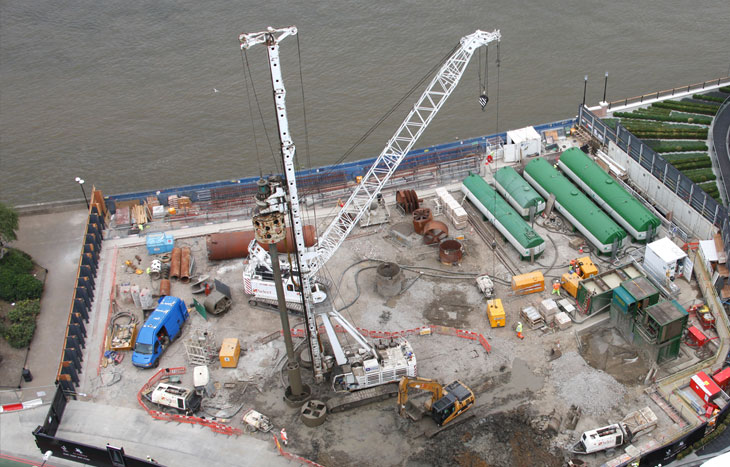
- SOUTHBANK PLACE
- NORTHERN LINE EXTENSION
- NINE ELMS SQUARE
- WOOD WHARF MARINE PILES
- CANARY WHARF CROSSRAIL STATIONBOX
- THE TOWER, 1 ST GEORGE WHARF
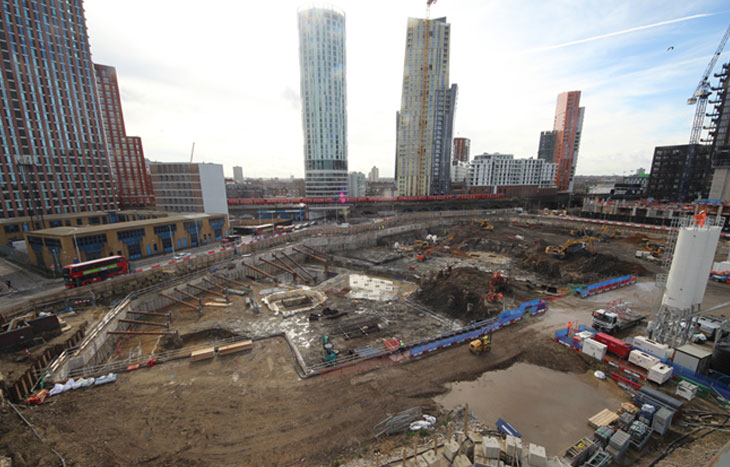
- 10 BANK STREET, CANARY WHARF
- NINE ELMS SQUARE
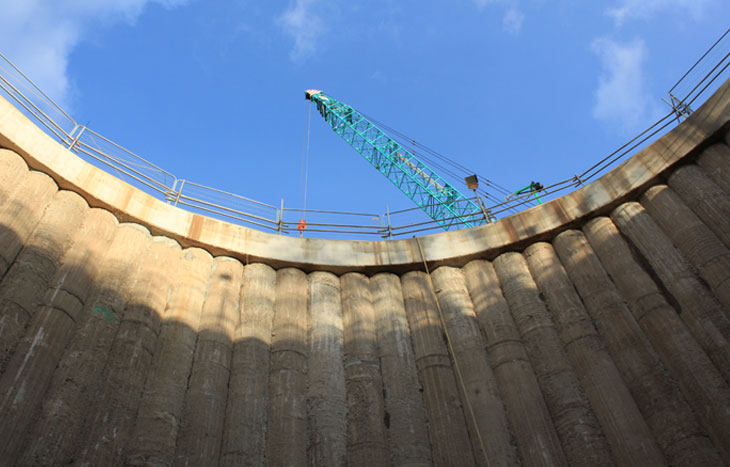
- 190 THE STRAND
- SOUTH QUAY PLAZA
- HATHERSHAW SHAFT
- THE FRANCIS CRICK INSTITUTE
- 177 BOTHWELL STREET
- SOHO PLACE
- EDINBURGH ST JAMES
- GRAPHANE ENGINEERING INNOVATION CENTRE
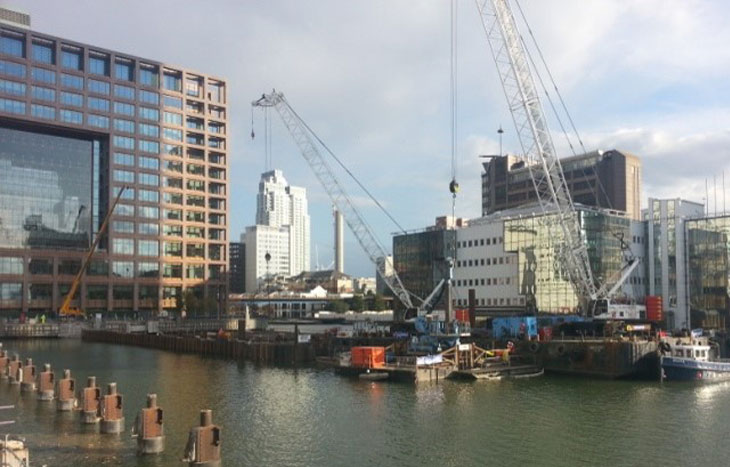
- 10 BANK STREET, CANARY WHARF
- TIDEWAY, BLACKFRIARS BRIDGE
- WOOD WHARF MARINE PILES
- CANARY WHARF CROSSRAIL STATIONBOX
Expanded Geotechnical completed the CFA Bored foundation piling at the Oxford Westgate Shopping Centre. The development comprised four blocks and piling was carried out on Block 3 and Block 4. The piling works were sequenced to follow behind the demolition and the archaeological works which introduced logistical challenges.
To meet the demanding programme a heavy-duty Bauer BG24 piling rig was used on the site for the different visits. The considerable overlap of trades required piling to be installed initially adjacent to live demolition and archaeological activities. This demanded a high level of cooperation, coordination and sequencing between trade packages.
As part of the first phase delivery team Expanded Geotechnical installed; 700 CFA bored secant piles, 1000 900mm and 600mm diameter CFA bearing piles, six preliminary piles to enable significant value engineering and removal of 75 existing 600mm diameter concrete piles, approximately 15m long.
A single-storey basement was constructed using 700 CFA bored secant piles with differing sizes of 750mm and 900mm diameter piles. The vertical load was also applied to the secant wall, increasing the length of the male piles to 32m. The deep CFA piles were founded into the Thames sand at approximately 28m below piling platform level.
Permanent and temporary 900mm diameter CFA plunge columns were installed to a tolerance of 1:100, the entire length of the reinforcement cage and column was in excess of 26.0m and vibrated to piling platform level.
We mobilised the most powerful CFA rig in our fleet to install 900mm diameter CFA bearing piles achieving a max socket of 4.5m into the Thanet Sands.
Cut-off levels for the 900mm diameter bearing piles were in excess of 13m below piling platform level, the cages were plunged to the correct level using our in-house designed cage plunger.
Expanded Geotechnical constructed 599no 900dia contiguous wall piles (11-15m, up to 9m rock sockets) for two large basements, and 284no 600dia bearing piles (8-12m) and twelve Tower Crane piles. We used our two largest CFA machines on this job, which can install piles up to 1200mm diameter and up to 34m long.
Our scope was completed ahead of our target and within budget – our client was extremely pleased with our performance. Through the project, drone photography was effectively used for progress meeting, client reporting and logistics planning.
Secured after a highly competitive tender competition, we completed the first phase of the bearing piles for Blocks A -J. These works involve the construction of CFA bearing piles 450mm and 600mm diameter up to 28m deep, along with the provision of selected attendances to the piling works supplied through our in-house plant company Select Plant Hire.
Working to an ambitious delivery programme Expanded have been able to accelerate the piling works allowing early start of substructure to facilitate an overall reduction in the project duration.
Expanded Geotechnical delivered this high-profile ground engineering project over the course of nine months. The first operation was the installation of a 150m-long king post wall positioned only 300mm from a large-diameter cast iron, highly sensitive Victorian gas main. After preliminary test piles were installed, the bentonite plant was commissioned and the diaphragm wall commenced. Two large- diameter piles existed on the line of the diaphragm wall.
Over 450 linear meters of wall were installed using rope grab diaphragm walling techniques. Over 250 large-diameter piles were installed, all with plunge columns to support a programme-saving top-down solution.
Expanded Geotechnical undertook the design and construction of a system of piled foundations to support the new Sewage Treatment Works infrastructure. The foundations consisted of CFA piles (Continuous Flight Auger) ranging from 450mm diameter to 900mm diameter, up to 28.0m deep. In addition, two other displacement-piling techniques were utilised to form some of the piled foundations to the structures. These were VCIS (vibro cast in situ) and DCIS (driven cast in situ). In total, 7,734 piles were constructed constituting a total of 73,261lin meters of pile. Almost 4,100m3 of concrete was consumed and almost 1,600 tonnes of steel reinforcement.
Both CFA and rotary bored techniques were used on the project. In total, 623nr CFA bearing piles were constructed, the majority which were 900mm piles, up to 23.5 meters long with a socket of 12m into the Thanet sand. All cages within the CFA piles were required to be full length of the pile once trimmed at cut off level. As cut off levels were nearly 7m below commencement level it was agreed a cage plunging method would be utilised. 11 rotary bored bearing piles were constructed within an area measuring 11m wide x 40m long using full length 1000mm segmental casing.
Appointed to install contiguous piles, bearing piles, crane bases and temporary works piles. This included 750mm contiguous piles to a depth of 14.5m, 142no. 600mm bearing piles to a max depth of 32.5m, 163no. 900mm bearing piles to a max depth of 32.5m, three working test piles – two to max load of 4.5MN and one to a max load of 6.0MN, two crane bases – one 8x900mm piles to a depth of 30m and one 4x600mm piles to a depth of 21m, and eight temporary works piles to a depth of 11.5m. The project was completed using two piling platform levels – 750mm contiguous wall from 5.3mOD and bearing piles from 2.1mOD. Our work was awarded the first-ever Blue safety inspection classification.
On this project, Expanded Geotechnical installed over 399 no. 1180/1000mm diameter secant wall piles using three piling rigs, along with 40no. 900mm diameter rotary bearing piles and 43no. 1500mm diameter rotary bored plunge column piles to support temporary works including tower crane and top down construction. The total bored length was approximately 10394m requiring approximately 9000m3 of concrete.
In areas where piling was close to perimeter hoarding, measures were taken to reduce the lengths of casings by splitting them in sections of 4m instead of 8m, to remove the risk of spoil falling over the site hoarding. Hoarding was also extended in height as an extra measure.
The project involved rotary bored piling using segmental casing to form a secant retaining wall and bearing piles, with plunge columns for top down basement construction. Majority of piles installed from B1 level.
Working around demolition works, which at times created limited access/egress. Pumping concrete from ground level and controlled specialist lifting around site was required to safely manage this.
Several pile locations also required coring through existing reinforced concrete slabs. Additional scope added to the contract whilst on site was the coring of a brickwork wall to enable the installation of a sheet piled retaining wall.
Canary Wharf was the first and only Crossrail station to be constructed over water. The base slab of the station is approximately 26m below water level. The first stage of construction involved the installation of 18m-long steel tubes with interlocking clutches to create a watertight cofferdam.
Utilising up to five piling rigs at peak, the second stage of the project included the installation of 2100mm diameter piles drilled to approximately 40m below dock bed level. Additionally, 1200mm diameter piles were drilled to act in tension below the base slab. To complete the perimeter, a secant wall was formed using 1200mm diameter piles founding in the Thanet Sand.
Scope included installation of 247no. polymer bearing piles 1200-900mm diameter to approx. 54.0m below piling mat level, 396lm of secant wall 880-1180mm in diameter with piles ranging from 17.0-31.0m below pile mat level, 104no 750mm & 302no 900mm diameter CFA bearing piles, along with 600 & 750 & 900mm diameter CFA bearing piles to provide foundation support to raft slab. We also provided attendances to piling operations, including UXO probing, removal of pile arisings and piling mat maintenance.
Expanded Geotechnical delivered this high-profile ground engineering project over the course of nine months. The first operation was the installation of a 150m-long king post wall positioned only 300mm from a large-diameter cast iron, highly sensitive Victorian gas main. After preliminary test piles were installed, the bentonite plant was commissioned and the diaphragm wall commenced. Two large- diameter piles existed on the line of the diaphragm wall.
Over 450 linear meters of wall were installed using rope grab diaphragm walling techniques. Over 250 large-diameter piles were installed, all with plunge columns to support a programme-saving top-down solution.
Piling works were delivered in two phases following the demolition and relocation of the Kennel Club.
All piling works were undertaken from inside the existing single-storey basement. A compact Casagrande B180 rig, heavy duty Bauer BG24 & BG30 and a Liebherr LB 36 rigs were all utilised to deliver the project.
Our remit included a secant retaining wall for a three-storey basement across two thirds of the site footprint, bearing piles with plunge columns, and temporary works contiguous piled wall to facilitate a phased construction sequence.
Using our in-house expertise we developed a bespoke lifting arrangement for constructing precast concrete plunge columns.
In order to create the deep basement required for the new Nine Elms Station Box, Expanded placed a total of 300 secant piles, 50 bearing piles and 30 steel plunge columns, using five different piling rigs over the course of the project (one of them the biggest in the UK) and three crawler cranes.
In addition to the piling works, more than 70 existing piles were encountered, which required removal to allow for the construction of the station box and avoid leaving any obstacles for the TBM transit. The secant wall works undertaken on this site have never been done before in the UK.
The project involved the construction of rotary bored secant piles and rotary bored piles for building two shafts and river wall.
Due to the high concrete strengths (over 40MPa after 7 days) on the hard-hard secant wall of the circular shaft, it was imperative to adopt the correct sequencing so the males piles could be relatively easy to drill.
The piling works on Cofferdam 2 were heavily influenced by being isolated from any road. As a result, all equipment and steel reinforcement have been delivered to site by barge. An extra challenge was the pumping of concrete into the piles from Cofferdam 1, over 240m away.
A basement was required in the enclosed back garden of a central London crescent being converted into 17 luxury apartments. The three- level basement provides parking spaces for 21 cars.
The key challenge for this project was access into the back garden area. The preferred option was to break out a ‘tunnel’ from the main road through the northern most terrace. The 4m wide by 16m long tunnel not only provided access for the rig but also the concrete pump hoses and a spoil conveyor. This novel site access contributed significantly to the piling works being completed approximately six weeks ahead of schedule.
Expanded Geotechnical delivered the very complex and challenging foundation package for the new Crossrail station at Liverpool Street. The scope of works included secant piled walls, contiguous piled walls drilled under support fluid, bearing piles and plunge column piles across diameters ranging 300mm to 1500mm and depths in excess of 50m. The plunge columns were up to 38m long, which were the longest installed in the UK at the time.
Surrounded by buildings and with piles constructed within 2m of the London Underground line, Expanded used a Bauer BG30 rig and Liebherr LTR1100 telescopic crawler crane supplied by Select Plant to install the works.
The project involved the installation of piles in multiple phases. Initially, tower crane and bearing piles were installed in the open basement before mobilising to ground level to continue bearing piles and install the contiguous wall. Thereafter, a restricted access rig was mobilised to complete bearing piles in the basement at ground level. Expanded piling were contracted for the works totalling almost 8000lm of piling and over 2500m3 of concrete.
Piling operations were phased around the demolition and construction works taking place across different elevations of the extension; this required detailed sequencing in conjunction with INTU and the local authorities.
The project involved creating a new stretch of railway line to allow separation of the slow and fast lines at Norton Bridge. To do this, a number of road / rail junctions and interfaces were constructed, some of which required piling work to support the new structures.
Piles for most structures were installed under Adjacent Line Open (ALO) conditions with stringent plans made and approved to safeguard the live West Coast Mainline.
Expanded Geotechnical also developed an auger cleaner system to bolster the performance of the standard wire auger cleaner. The auger cleaner used jets of compressed air and water to thoroughly clean the auger before it reached significant height.
In order to create the deep basement required for the new Nine Elms Station Box, Expanded placed a total of 300 secant piles, 50 bearing piles and 30 steel plunge columns, using five different piling rigs over the course of the project (one of them the biggest in the UK) and three crawler cranes.
In addition to the piling works, more than 70 existing piles were encountered, which required removal to allow for the construction of the station box and avoid leaving any obstacles for the TBM transit. The secant wall works undertaken on this site have never been done before in the UK.
Expanded Geotechnical delivered this high-profile ground engineering project over the course of nine months. The first operation was the installation of a 150m-long king post wall positioned only 300mm from a large-diameter cast iron, highly sensitive Victorian gas main. After preliminary test piles were installed, the bentonite plant was commissioned and the diaphragm wall commenced. Two large- diameter piles existed on the line of the diaphragm wall.
Over 450 linear meters of wall were installed using rope grab diaphragm walling techniques. Over 250 large-diameter piles were installed, all with plunge columns to support a programme-saving top-down solution.
The project involved the construction of rotary bored secant piles and rotary bored piles for the construction of a CSO shaft, Interception chamber and bearing piles as part of the Thames Tideway project.
On this project, Expanded Geotechnical are installing 880 piles in the CSO shaft & interception chamber, along with 600mm bearing piles with the BG30 piling rig.
Despite the complex working environment, Expanded Geotechnical have taken a proactive approach to managing safety on site, with excellent segregation shown at all times along with a strong duty of care to follow-on trades.
The project involved the construction of rotary bored secant piles and rotary bored piles for building two shafts and river wall.
Due to the high concrete strengths (over 40MPa after 7 days) on the hard-hard secant wall of the circular shaft, it was imperative to adopt the correct sequencing so the males piles could be relatively easy to drill.
The piling works on Cofferdam 2 were heavily influenced by being isolated from any road. As a result, all equipment and steel reinforcement have been delivered to site by barge. An extra challenge was the pumping of concrete into the piles from Cofferdam 1, over 240m away.
A key feature of the site is the deep and extensive excavations. The excavations are 9-11m deeper on the north side of the site compared to the south, due to the hillside location. The other main constraint of this project was working in close proximity to the live hospital buildings.
On this project, Expanded Geotechnical installed 325no. 900mm diameter contiguous wall piles using one piling rigs, along with 81 no. 600mm diameter rotary bored bearing piles and 6 no. 900mm diameter piles to support temporary works. The total bored length on the project was approximately 8800m requiring approximately 5500m3 of concrete.
In addition, 28 no. 450mm diameter open bored mini piles were constructed for a car park entrance.
Expanded Geotechnical was the contractor selected to deliver a basement over the site footprint, installing a rotary bored secant wall, incorporating plunge column bored piles. All piles were installed from a working platform within the existing basement approximately 3m below road level.
The existing retaining wall on the Victoria Street elevation was propped using steel raking props and thrust blocks.
As the line of the secant wall progressed under the line of these props, the working area became restricted. The temporary works solution required the raking props to be replaced by king posts cast into the head of male secant piles. To meet a demanding programme, two heavy-duty Bauer drilling rigs were used.
The project involved rotary bored piling using segmental casing to form a secant retaining wall and bearing piles, with plunge columns for top down basement construction. Majority of piles installed from B1 level.
Working around demolition works, which at times created limited access/egress. Pumping concrete from ground level and controlled specialist lifting around site was required to safely manage this.
Several pile locations also required coring through existing reinforced concrete slabs. Additional scope added to the contract whilst on site was the coring of a brickwork wall to enable the installation of a sheet piled retaining wall.
Edinburgh St James is a 1.7 million sq ft city centre development and one of the biggest regeneration projects currently underway in the UK. Construction for Edinburgh St James started in 2016 with completion due in 2020.
The scope includes 548no secant piles, 127no bearing piles and 13no cofferdam piles.
The foundation works on St James Quarters started in December 2016. The programme for the piled element of the basement was initially 66 working weeks, with up to four piling rigs working simultaneously. The number of rigs required to achieve the current program is based on achieving a drilling rate in hard rock of 1m/hr.
On this project, Expanded Geotechnical installed over 399 no. 1180/1000mm diameter secant wall piles using three piling rigs, along with 40no. 900mm diameter rotary bearing piles and 43no. 1500mm diameter rotary bored plunge column piles to support temporary works including tower crane and top down construction. The total bored length was approximately 10394m requiring approximately 9000m3 of concrete.
In areas where piling was close to perimeter hoarding, measures were taken to reduce the lengths of casings by splitting them in sections of 4m instead of 8m, to remove the risk of spoil falling over the site hoarding. Hoarding was also extended in height as an extra measure.
The project involved the construction of rotary bored secant piles and rotary bored plunge column piles for two basements as part of the Soho Place development. Expanded Geotechnical installed over 305no. 750mm diameter secant wall piles using two piling rigs, along with nine 1200mm diameter rotary bored plunge column piles to support temporary works. The total bored length on the project was approximately 4400m requiring approximately 2200m3 of concrete.
The secant wall piles were installed above a large number of underground assets, including Tottenham Court Road station, Central line tunnels and Elizabeth line tunnels.
Canary Wharf was the first and only Crossrail station to be constructed over water. The base slab of the station is approximately 26m below water level. The first stage of construction involved the installation of 18m-long steel tubes with interlocking clutches to create a watertight cofferdam.
Utilising up to five piling rigs at peak, the second stage of the project included the installation of 2100mm diameter piles drilled to approximately 40m below dock bed level. Additionally, 1200mm diameter piles were drilled to act in tension below the base slab. To complete the perimeter, a secant wall was formed using 1200mm diameter piles founding in the Thanet Sand.
The construction of the piling works undertaken on this site were focused on delivering a high quality product on a short period of time whilst keeping very high health and safety standards.
In order to create the 10m double basement required for the latest building of the Wandsworth Riverside Quarter, Expanded placed a total of 245 secant piles, 156 bearing piles and 4 tower crane piles, using one piling rig and one crawler crane and a very experience site crew.
The works took place on proximity to occupied buildings of residential nature. Careful planning allowed us to carry out the piling works without disturbing the neighbours and reducing production.
In order to create the deep basement required for the new Nine Elms Station Box, Expanded placed a total of 300 secant piles, 50 bearing piles and 30 steel plunge columns, using five different piling rigs over the course of the project (one of them the biggest in the UK) and three crawler cranes.
In addition to the piling works, more than 70 existing piles were encountered, which required removal to allow for the construction of the station box and avoid leaving any obstacles for the TBM transit. The secant wall works undertaken on this site have never been done before in the UK.
Expanded Geotechnical completed the rotary bored piling at Wood Wharf. The piling works for this project included marine piling under polymer. All the 143no piles were installed from a barge.
Positioning the barge was critical to ensure the piling rig could access the pile positions in the agreed orientation and proximity to the existing combi wall.
A number of the marine piles were designed to partially support one of the land based buildings and therefore these piles were required to be base grouted following the pile installation.
The remaining marine piles were used to support a precast concrete deck upon which parks and walkways were installed.
Expanded Geotechnical completed the rotary bored secant pile wall for a two-level basement at the Brunel Building at North Wharf Road, adjacent to Paddington Station, London. The piling works for this project included shallow piles above the LUL tunnels and deep piles near the LUL tunnels and the Grand Union Canal wall.
The 502no secant piles were installed from two different levels. All female piles were drilled 10m below the piling platform level into the London clay. The male piles at the Brunel Building ranged in depths between 10m to 28m below the platform level.
We utilised two heavy duty Bauer BG30 piling rigs on the site to deliver the demanding programme.
Expanded Geotechnical are constructing the bearing and contiguous wall piles for the new 11-storey new Google UK headquarters building alongside Kings Cross mainline train station.
This is a confined and restricted site bound by Kings Cross mainline train station on one side, with offices and roads bounding the other two. The project required extensive monitoring procedures in place to protect both the original Kings Cross train shed, and the access road into the station itself. There are also 99nr in-between king post and plunge columns installed to tight tolerances.
In order to create the deep basement required for the new Nine Elms Station Box, Expanded placed a total of 300 secant piles, 50 bearing piles and 30 steel plunge columns, using five different piling rigs over the course of the project (one of them the biggest in the UK) and three crawler cranes.
In addition to the piling works, more than 70 existing piles were encountered, which required removal to allow for the construction of the station box and avoid leaving any obstacles for the TBM transit. The secant wall works undertaken on this site have never been done before in the UK.
Phase II building in the city centre for the University of Oxford, compromising a 2-level substructure basement and 4 floors above ground.
This Phase II required the connection into the piled-wall of the ‘New Biochemistry’ building alongside. A 100mm gap was designed into the pile layout so that transversal vibrations wouldn’t be directed into the existing structure.
The 750mm secant wall was installed consistently with a segmental cased rotary bored technique, sealing into the firm Oxford Clay before progressing the drilling tools beyond the cased depth. Firm primary piles were installed ahead of the hard-secondary piles to create a retaining wall strong whilst forming a water-tight box across its entire surround.
To complete the scope a range of piling techniques and equipment will required with multiple piling rigs across the site. Scope included installation of 247no. polymer bearing piles 1200-900mm diameter to approx. 54.0m below piling mat level, 396lm of secant wall 880-1180mm in diameter with piles ranging from 17.0-31.0m below pile mat level, 104no 750mm & 302no 900mm diameter CFA bearing piles, along with 600 & 750 & 900mm diameter CFA bearing piles to provide foundation support to raft slab. We also provided attendances to piling operations, including UXO probing, removal of pile arisings and piling mat maintenance.
This high-profile site is at the entrance to the University Parks and is opposite Sir William Butterfield’s Grade 1 listed Keble College Chapel.
In total 223 secant piles were constructed. The walls for the main basement were formed by 880mm piles up to 24 metres long. These consisted of 114 female piles up to 17 metres long and 109 male piles up to 24 metres long.
There was a 16-metre retained height with two levels of props with ground anchors. In addition, the Delmag RH28 installed 20no bearing piles 880 mm x 24 metres long and for the tower crane base piles 4 piles 880mm x 26 metres long.
Edinburgh St James is a 1.7 million sq ft city centre development and one of the biggest regeneration projects currently underway in the UK. Construction for Edinburgh St James started in 2016 with completion due in 2020.
The scope includes 548no secant piles, 127no bearing piles and 13no cofferdam piles.
The foundation works on St James Quarters started in December 2016. The programme for the piled element of the basement was initially 66 working weeks, with up to four piling rigs working simultaneously. The number of rigs required to achieve the current program is based on achieving a drilling rate in hard rock of 1m/hr.
The Blackfriars Bridge Foreshore site is located on the north bank of the river Thames. All piling works were undertaken from jack-up barges within the river. In order to prevent bored material from the piles entering the river, specially designed casing funnels were used to prevent spillage.
One section of the work site piling was near the Waterloo and City Underground tube line and these works were carried out during engineering hours throughout the night. Extensive measures were put in place to ensure minimal sound and noise pollution because of the close proximity of residents.
With the exception of concrete, all deliveries were by barge from Tilbury or Northfleet Dock.
The EAAR was part of the Infrastructure Programme Eastern Apron Development, to provide the main operational and strategic road link across the Eastern Apron. The scope includes construction of a 770m airside road & taxi lane underpass linking T2A with T2B & T2C stands, two tunnels of 110m length and 12m width to allow two opposing carriageways, and secant piling retaining walls and pile capping beam.
A key point to note is the close proximity of the Piccadilly Underground Line with the EAAR going over the top of the tunnel. There were important working regulations to adhere to, ensuring effective monitoring of ground movement, and liaison with London Underground.
Expanded Geotechnical were awarded the package to install contiguous CFA wall piles, and to carry out the installation of CFA bearing piles at basement level, to form the foundations for three new residential blocks (33, 16 and 11 storeys respectively).
Around 10km of piles were drilled, all of which were founded into the Manchester sandstone, and around 4500m3 of concrete was cast into piles.
The site was located adjacent to a live residential building. Due to the restricted access at site, the rig and crane deliveries had to be planned thoroughly.
Expanded Geotechnical completed the rotary bored piling at Wood Wharf. The piling works for this project included marine piling under polymer. All the 143no piles were installed from a barge.
Positioning the barge was critical to ensure the piling rig could access the pile positions in the agreed orientation and proximity to the existing combi wall.
A number of the marine piles were designed to partially support one of the land based buildings and therefore these piles were required to be base grouted following the pile installation.
The remaining marine piles were used to support a precast concrete deck upon which parks and walkways were installed.
Scope included installation of 247no. polymer bearing piles 1200-900mm diameter to approx. 54.0m below piling mat level, 396lm of secant wall 880-1180mm in diameter with piles ranging from 17.0-31.0m below pile mat level, 104no 750mm & 302no 900mm diameter CFA bearing piles, along with 600 & 750 & 900mm diameter CFA bearing piles to provide foundation support to raft slab. We also provided attendances to piling operations, including UXO probing, removal of pile arisings and piling mat maintenance.
Canary Wharf was the first and only Crossrail station to be constructed over water. The base slab of the station is approximately 26m below water level. The first stage of construction involved the installation of 18m-long steel tubes with interlocking clutches to create a watertight cofferdam.
Utilising up to five piling rigs at peak, the second stage of the project included the installation of 2100mm diameter piles drilled to approximately 40m below dock bed level. Additionally, 1200mm diameter piles were drilled to act in tension below the base slab. To complete the perimeter, a secant wall was formed using 1200mm diameter piles founding in the Thanet Sand.
In order to create the deep basement required for the new Nine Elms Station Box, Expanded placed a total of 300 secant piles, 50 bearing piles and 30 steel plunge columns, using five different piling rigs over the course of the project (one of them the biggest in the UK) and three crawler cranes.
In addition to the piling works, more than 70 existing piles were encountered, which required removal to allow for the construction of the station box and avoid leaving any obstacles for the TBM transit. The secant wall works undertaken on this site have never been done before in the UK.
142 piles of 900mm and 1000mm diameter were constructed to support loads imposed by the new office building.
The pile design required piles to be socketed up to 4m into the underlying bedrock – due to the level of the bedrock, this required temporary casing lengths up to 26m. In order to achieve this level of penetration and to take account of the varying pile lengths and bedrock levels, segmental temporary casing was used, fitted with cutting shoes that could penetrate into the bedrock. To handle and install these substantial casing lengths we utilised 2 of our largest and most powerful hydraulic piling rigs – the Bauer BG36 and BG42 models.
The project involved the construction of the rotary bored secant piles and rotary bored bearing piles for the construction of 8nos. low to medium rise buildings. Expanded Geotechnical installed over 500 piles with diameters ranging from 750mm to 2100mm. The total bored length on the project was approximately 14500m requiring approximately 15,600m3 of concrete and generating 14,700m3 of muck.
The majority of the rotary bored piles were constructed to standard tolerances, to the exception of the piles adjacent to LUL assets, which were constructed to 25mm positional tolerance and to 1 in 200 verticality.
To complete the scope a range of piling techniques and equipment will required with multiple piling rigs across the site. Scope included installation of 247no. polymer bearing piles 1200-900mm diameter to approx. 54.0m below piling mat level, 396lm of secant wall 880-1180mm in diameter with piles ranging from 17.0-31.0m below pile mat level, 104no 750mm & 302no 900mm diameter CFA bearing piles, along with 600 & 750 & 900mm diameter CFA bearing piles to provide foundation support to raft slab. We also provided attendances to piling operations, including UXO probing, removal of pile arisings and piling mat maintenance.
To facilitate the construction of two new buildings within the Canary Wharf Estate, the construction of a double skin-tied cofferdam was required to provide temporary retention of the dock water.
The double skin cofferdam was approximately 170 linear meters in length. This comprised 242No 22m long AZ36-700N sheet piles, which form the two main walls (or skins) and 88No 16m long AZ36-700N sheet piles acting as cross walls between the two main sheet pile walls.
The sheet piles were primarily installed using a Giken Super crush silent piler due to the sites location adjacent to both commercial and residential properties.
The project involved the construction of rotary bored secant piles and rotary bored plunge column piles for two basements as part of the Soho Place development. Expanded Geotechnical installed over 305no. 750mm diameter secant wall piles using two piling rigs, along with nine 1200mm diameter rotary bored plunge column piles to support temporary works. The total bored length on the project was approximately 4400m requiring approximately 2200m3 of concrete.
The secant wall piles were installed above a large number of underground assets, including Tottenham Court Road station, Central line tunnels and Elizabeth line tunnels.
Edinburgh St James is a 1.7 million sq ft city centre development and one of the biggest regeneration projects currently underway in the UK. Construction for Edinburgh St James started in 2016 with completion due in 2020.
The scope includes 548no secant piles, 127no bearing piles and 13no cofferdam piles.
The foundation works on St James Quarters started in December 2016. The programme for the piled element of the basement was initially 66 working weeks, with up to four piling rigs working simultaneously. The number of rigs required to achieve the current program is based on achieving a drilling rate in hard rock of 1m/hr.
The site, located within the grounds of Manchester University’s North Campus came with a complex set of historical and technical challenges. The brownfield site had seen many heavy industrial uses over the last 2 centuries and even had a buried bridge structure beneath the building footprint.
To reduce the number of piling rig mobilisations, we utilised a dual- purpose rig, the Bauer BG24. We installed all the CFA piles and then converted the rig on site (in a single shift) to install rotary bored piles. Obstructions were cored using our segmental casings fitted with cutting shoes, core barrels and extra heavy-duty rock drilling augers and buckets.
142 piles of 900mm and 1000mm diameter were constructed to support loads imposed by the new office building.
The pile design required piles to be socketed up to 4m into the underlying bedrock – due to the level of the bedrock, this required temporary casing lengths up to 26m. In order to achieve this level of penetration and to take account of the varying pile lengths and bedrock levels, segmental temporary casing was used, fitted with cutting shoes that could penetrate into the bedrock. To handle and install these substantial casing lengths we utilised 2 of our largest and most powerful hydraulic piling rigs – the Bauer BG36 and BG42 models.
We completed the piling, sunstructure and construction of a complex three storey basement. The substructure is enclosed by a 300m-long secant wall constructed of 400 piles, the basement is founded on 140 bearing piles. Construction of level B3 involved installing a 3m deep raft foundation using a single concrete pour of 3,300m3. Precast panels were then used to form passenger/vehicle lift cores up to ground level to access the hotel. Infill floor areas were completed using reinforced concrete slabs. The concrete raft pour was delivered a week ahead of schedule. The pour took only 24 hours to complete with two teams working in shifts.
Expanded carried out the design and construction of a secant piled circular shaft with an internal diameter of 25.4m and planned excavation depth of 20m. The shaft was part of the Medlock Water Quality Programme and was designed as an Unintentional Intermittent Discharge (UID) Tank.
The challenging geometry of the shaft required both female and male piles to achieve a design concrete strength of C32/40. Our in-house team developed an installation sequence and a female concrete mix, ensuring the female piles could be cut without damage and causing excessive wear to the drilling tools.
Permanent and temporary 900mm diameter CFA plunge columns were installed to a tolerance of 1:100, the entire length of the reinforcement cage and column was in excess of 26.0m and vibrated to piling platform level.
We mobilised the most powerful CFA rig in our fleet to install 900mm diameter CFA bearing piles achieving a max socket of 4.5m into the Thanet Sands.
Cut-off levels for the 900mm diameter bearing piles were in excess of 13m below piling platform level, the cages were plunged to the correct level using our in-house designed cage plunger.
The project involved the development of the site known as The Strand within the City of Westminster into a new high-quality residential development over an existing two-level basement. The piling works were undertaken over six different platform levels to cope with the sloping nature of the site.
The works constituted the deepest 880mm diameter rotary-cased basement undertaken by Expanded, within a very constricted site in the heart of the city. We received several safety awards from the client throughout the duration of the project and the quality of the works was praised by the client.
Canary Wharf was the first and only Crossrail station to be constructed over water. The base slab of the station is approximately 26m below water level. The first stage of construction involved the installation of 18m-long steel tubes with interlocking clutches to create a watertight cofferdam.
Utilising up to five piling rigs at peak, the second stage of the project included the installation of 2100mm diameter piles drilled to approximately 40m below dock bed level. Additionally, 1200mm diameter piles were drilled to act in tension below the base slab. To complete the perimeter, a secant wall was formed using 1200mm diameter piles founding in the Thanet Sand.
Expanded Geotechnical completed the rotary bored pilling at Wood Wharf. The pilling works for this project included marine pilling under polymer. All the 143no piles were installed from a barge.
Positioning the barge was critical to ensure the pilling rig could access the pile positions in the agreed orientation and proximity to the existing combi wall.A number of the marine piles were designed to partially support one of the land based buildings and therefore these piles were required to be base grouted following the pile installation.
The remaining marine piles were used to support a precast concrete deck upon which parks and walkways were installed.
The Blackfriars Bridge Foreshore site is located on the north bank of the river Thames. All piling works were undertaken from jack-up barges within the river. In order to prevent bored material from the piles entering the river, specially designed casing funnels were used to prevent spillage.
One section of the work site piling was near the Waterloo and City Underground tube line and these works were carried out during engineering hours throughout the night. Extensive measures were put in place to ensure minimal sound and noise pollution because of the close proximity of residents.
With the exception of concrete, all deliveries were by barge from Tilbury or Northfleet Dock.
To facilitate the construction of two new buildings within the Canary Wharf Estate, the construction of a double skin-tied cofferdam was required to provide temporary retention of the dock water.
The double skin cofferdam was approximately 170 linear meters in length. This comprised 242No 22m long AZ36-700N sheet piles, which form the two main walls (or skins) and 88No 16m long AZ36-700N sheet piles acting as cross walls between the two main sheet pile walls.
The sheet piles were primarily installed using a Giken Super crush silent piler due to the sites location adjacent to both commercial and residential properties.
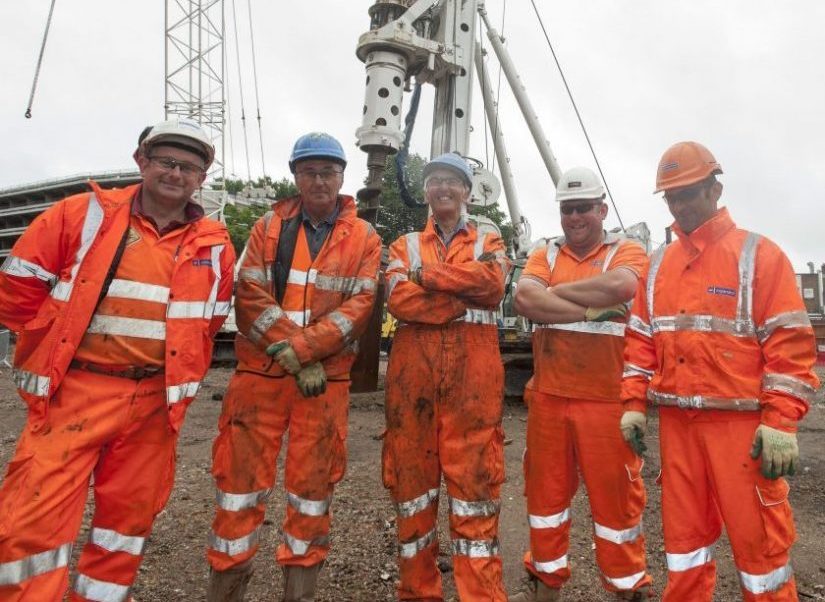